Sterilisation of liquids and culture media used in high throughput screening
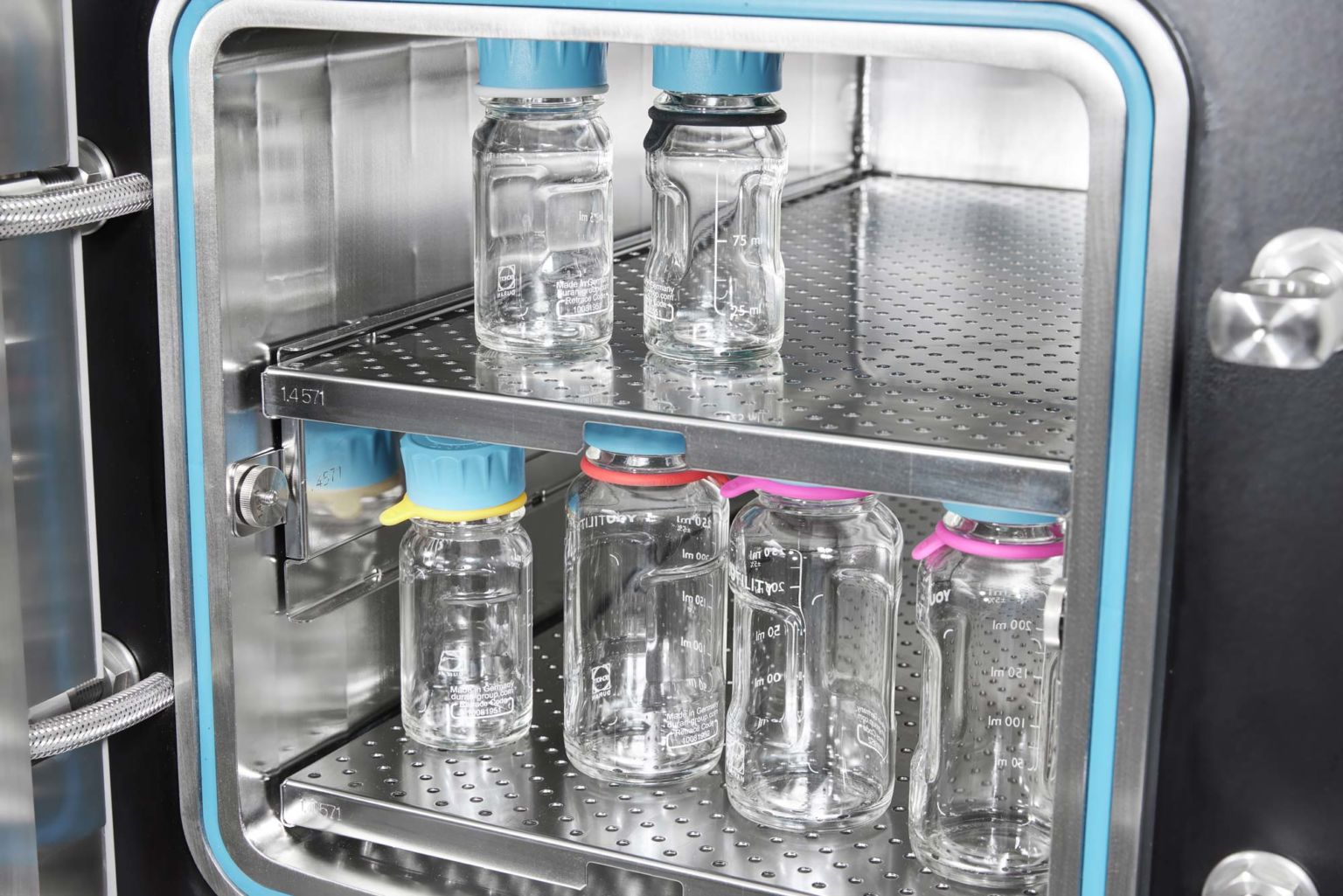
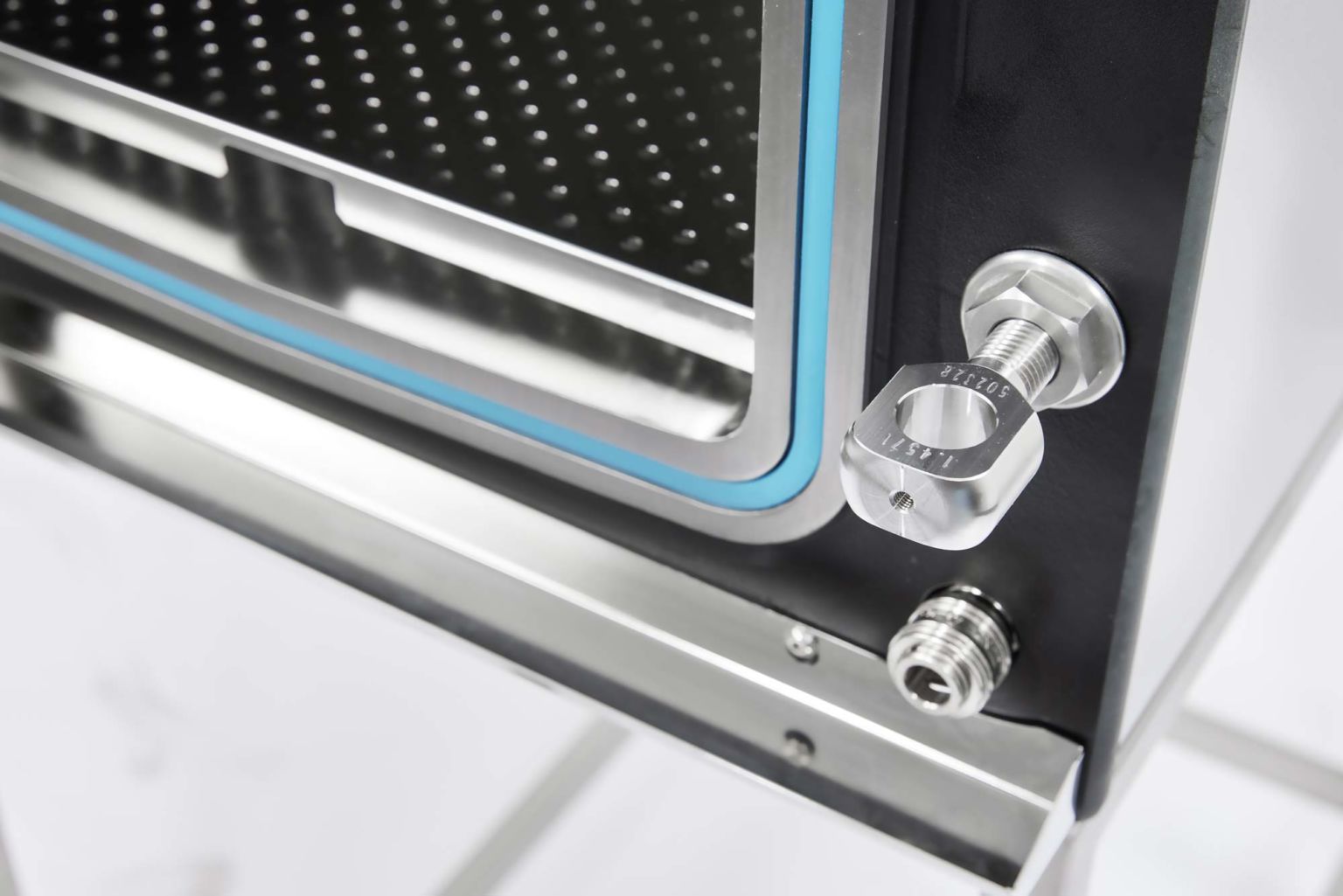
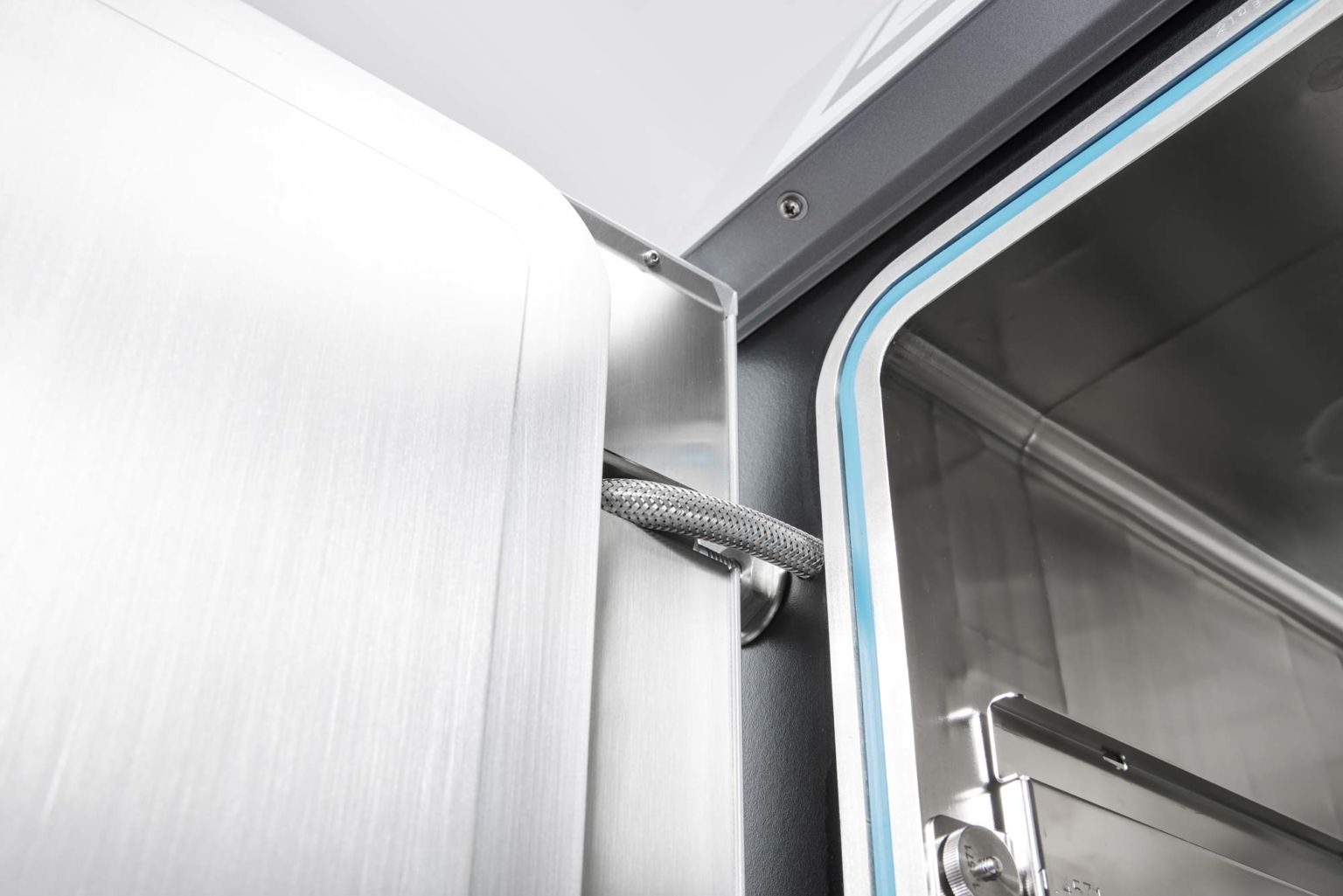
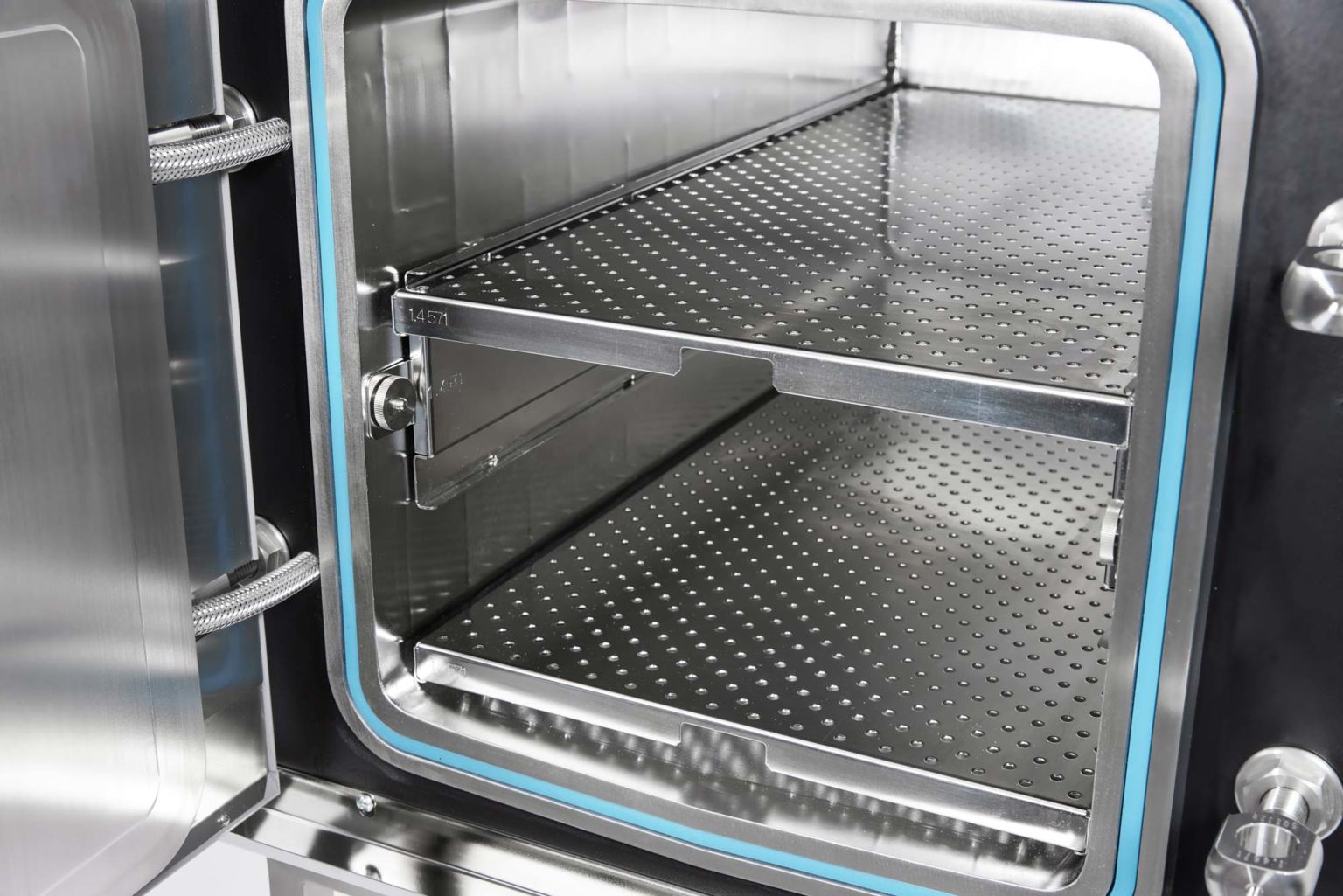
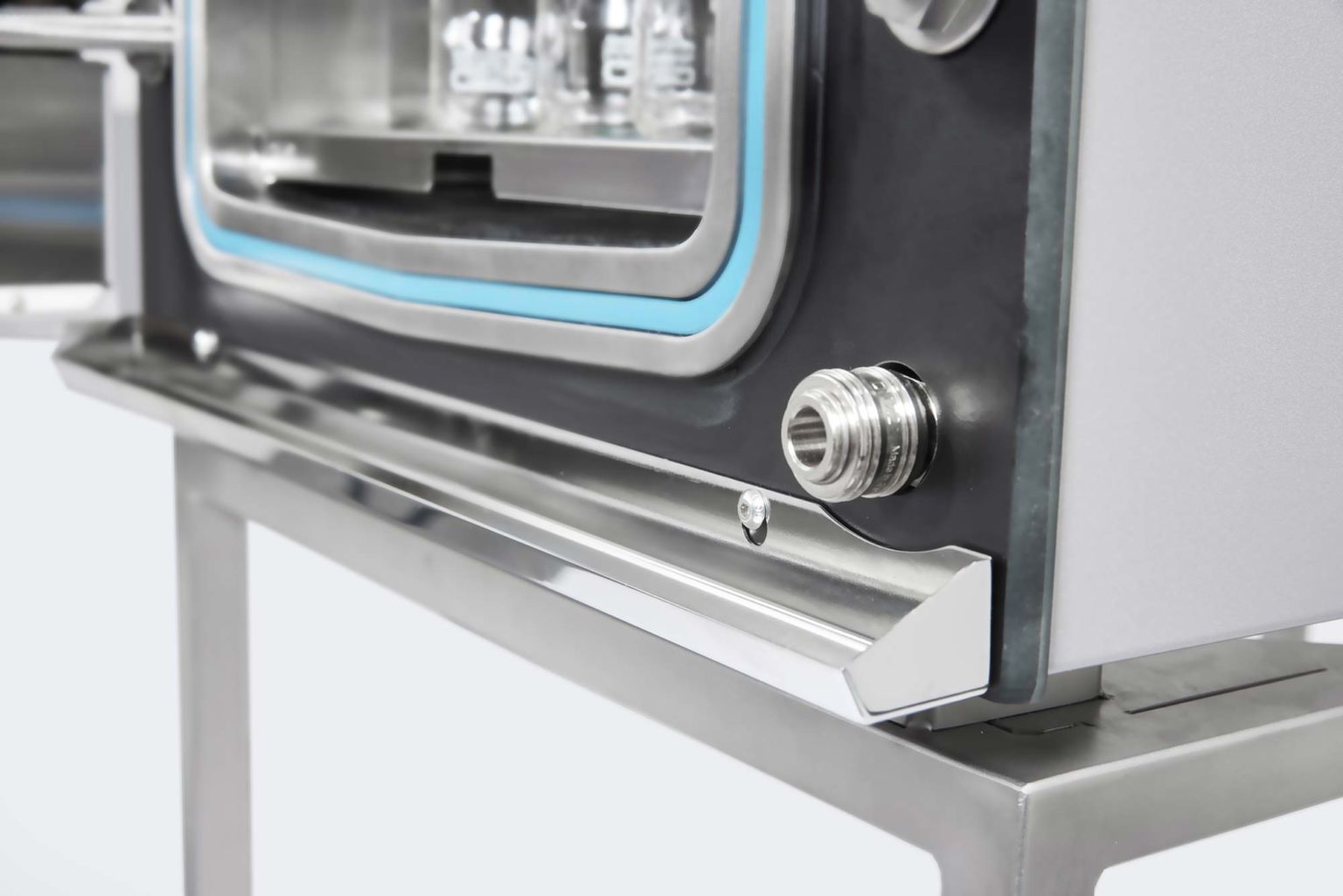
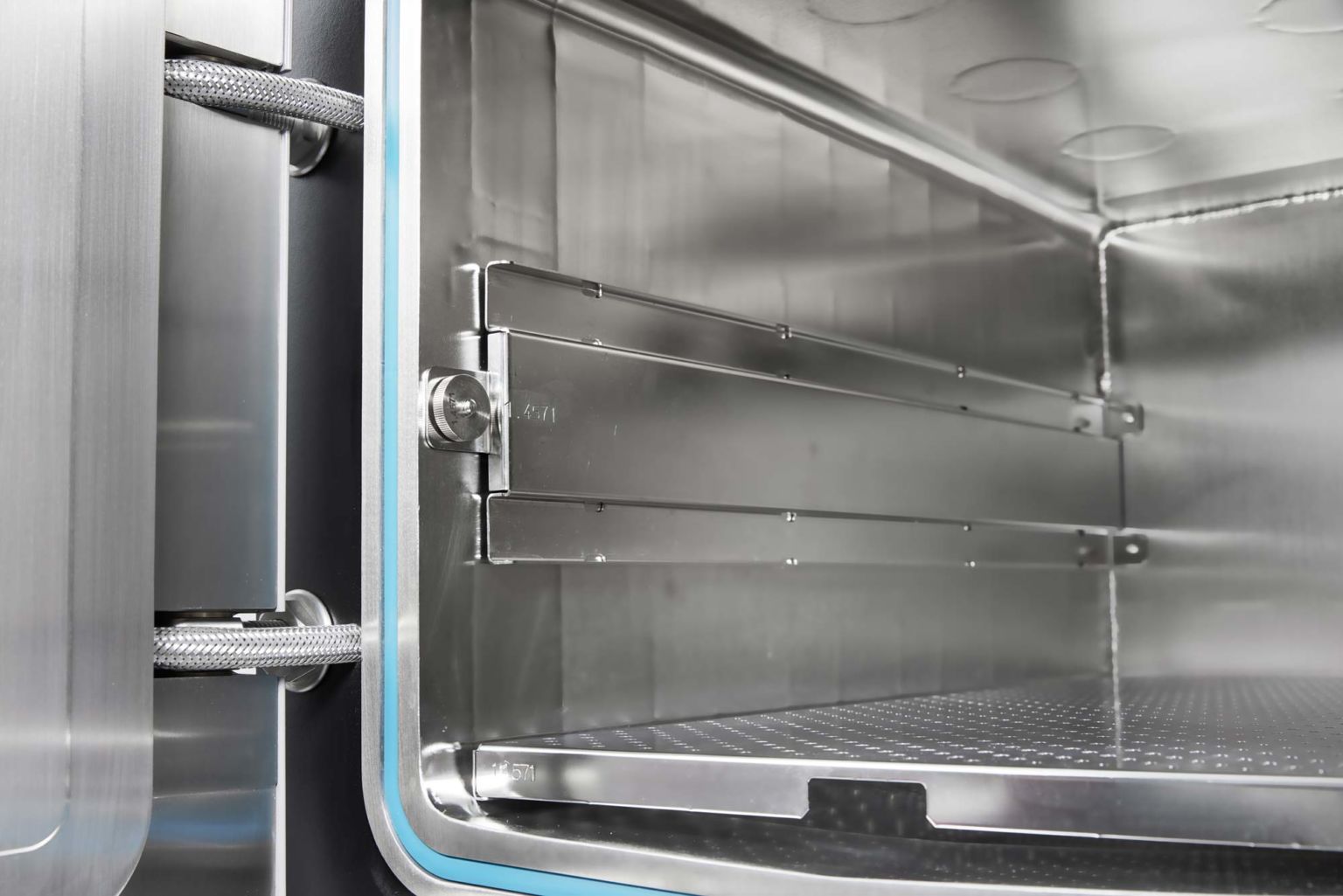
- Long service life
- Quality
- Premium customer service
- High rate of load cycles
- Full stainless steel housing
- Low working height
Innovative
Advanced
Attractive
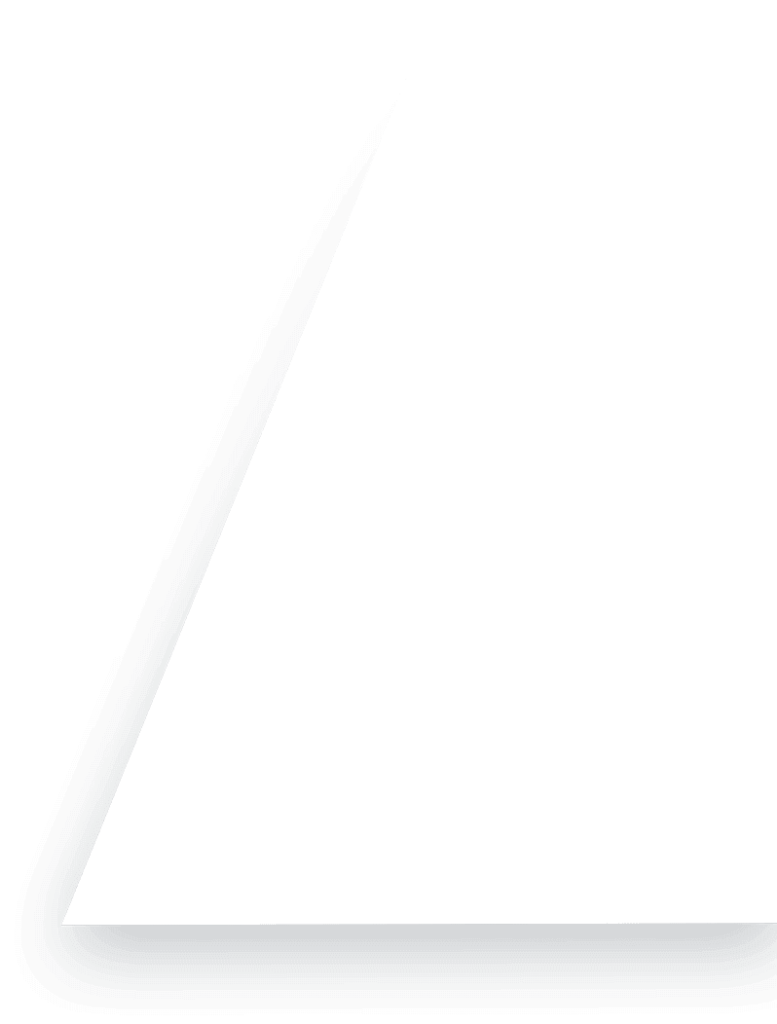
Excellence in autoclaves
Huge capacity on a small footprint with a space-saving hinged door. The usable space inside the VARIOKLAV® benchtop autoclave is free of heating elements and feed water. Compact benchtop autoclaves with 25 and 195-litre loading capacities using a design that saves as much space as possible.
Suitable for liquids, consumables and process equipment, as well as laboratory waste, genetically modified substances and long-term testing of items under steam.
- Insulation using open-cell Basotec
- Valves controlled pneumatically (greater closing force)
- Floor drain valve in the sterilisation chamber, no contaminated water can escape
- Sterile filter cartridge in stainless steel lid is installed upright, no residual water left in the filter
- Very powerful liquid-ring vacuum pump
Your enquiry
Any questions? We will be delighted to help you and will respond to your enquiry as soon as possible!
Your enquiry is of course free of charge and without obligation!
Key features
VARIOKLAV® BlueLine is a range of top-quality basic equipment perfectly designed to cover all routine tasks in a microbiology laboratory. Our steam sterilisers work reliably and quickly. VARIOKLAV BlueLine autoclaves are among the best-selling steam sterilisers in their class in Germany.
- RAPID COOLING - short cooling time thanks to the welded double jacket
- PRE-VACUUM AND DRYING - low energy / low consumption/ low supply voltage
- EMISSION-FREE STERILISATION - rapid warm-up time thanks to process-matched heat generation
- PROCESS DOCUMENTATION
Special functions of the Varioklav Blueline
Control
- Temperature-controlled venting system
- Exact operating temperature setting
- Separate control and safety circuits Temperature sensing using three-wire technology
- Configure, lock and approve sterilisation cycles
- Sterilisation data recorded using integrated dot matrix printer or Segosoft software
- Temperature controlled media processes for/using liquids
Sterile pressure support
Vapour pressure drops during the cooling phase. The pressure drop as the sterilising steam cools is compensated for using compressed air (pressure support) which can also be supplied sterile as an option. The pressure support air is fed in through a pressure-tight stainless steel filter housing.
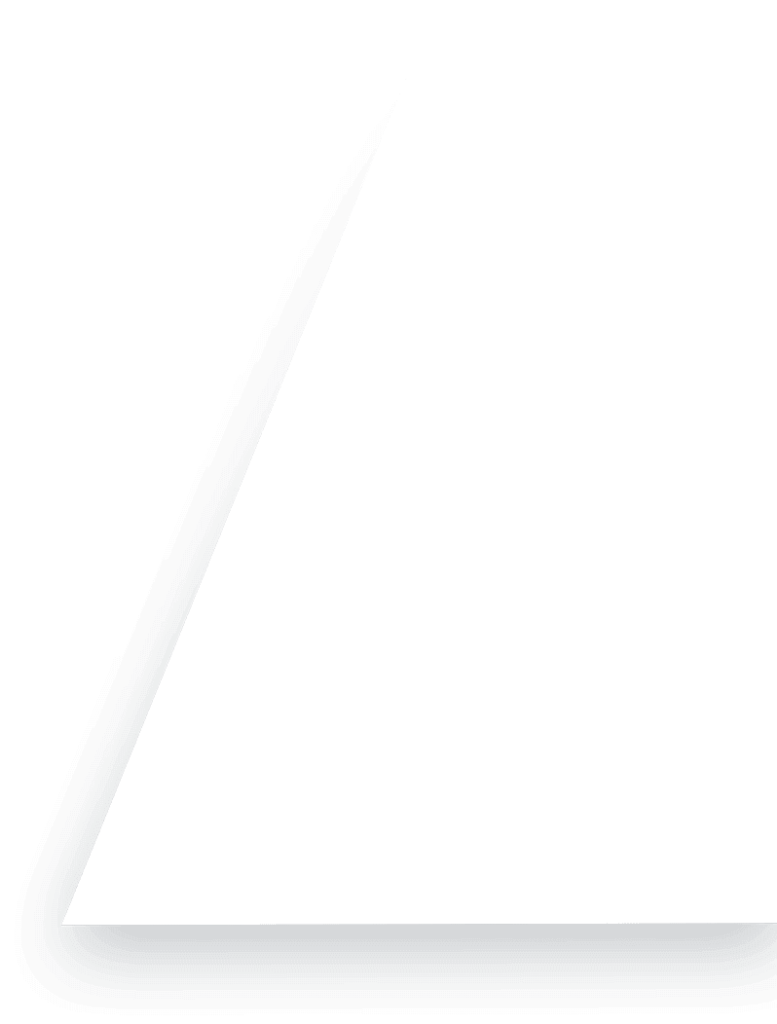
Recooling and rapid cooling
The cooling modules significantly reduce the autoclave cooling down time. This enables higher throughput rates for batch processing. Depending on the cycle and how the autoclave is loaded, cooling times from 5 to 80 minutes are possible.
- Media temperature control: highly flexible, robust media sensor for precise setting of sterilisation temperature in the medium and control of exposure time
- Radial fan Ø 180 mm, 80 watts
- Easy to replace when servicing
- Sensor interruption and short circuit display
- Cooling water consumption: 15 – 40 litres
- Programmable sterilisation cycles
- Shelves can be loaded into four height-adjustable positions
Recording sterilisation data
To verify the sterilisation process has run successfully when conducting quality assurance, data from the sterilisation process can be viewed using an integrated dot matrix printer or using the Segosoft software.
- Shorter cooling time compared to natural cooling: by at least 40% even for large containers
- No additional post-installation connections
- Connection to deionised water, soft water or in-house cooling water circuit for cooling
- 100% reliable destruction of pathogens
- Pressure vessel, TÜV certified, manufactured in accordance with the Pressure Equipment Directive and other European regulations
- CE marked under Low Voltage Directive
- 90% of the jacket space is cooled
- Additional pressure monitoring
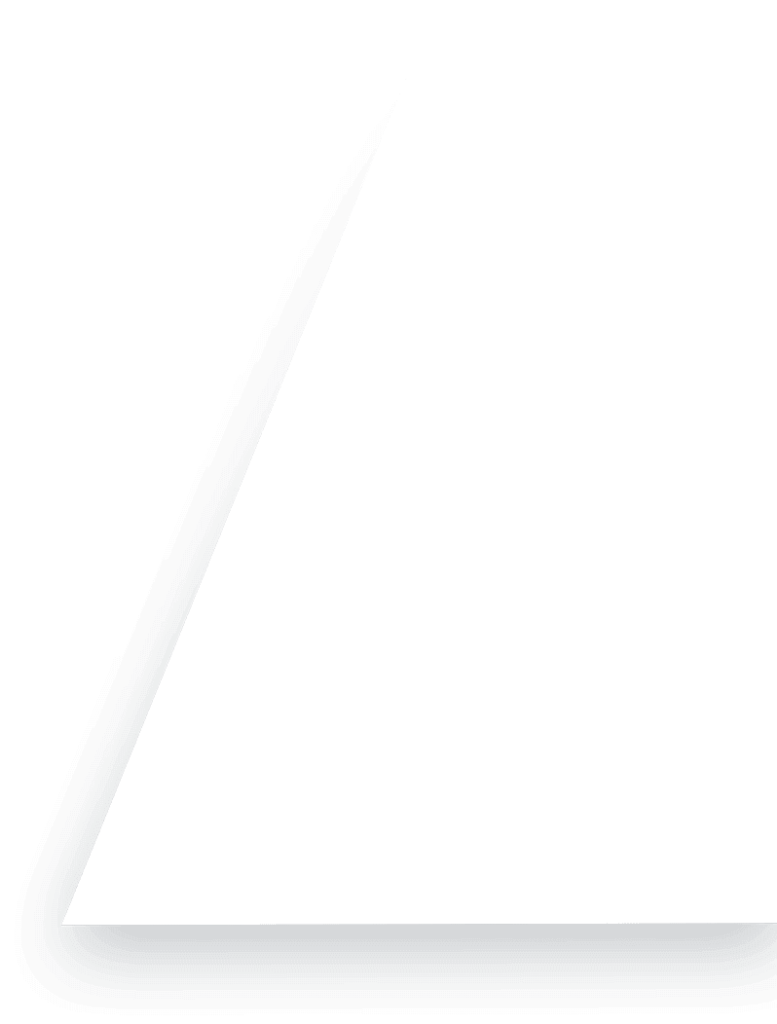
What our customers say
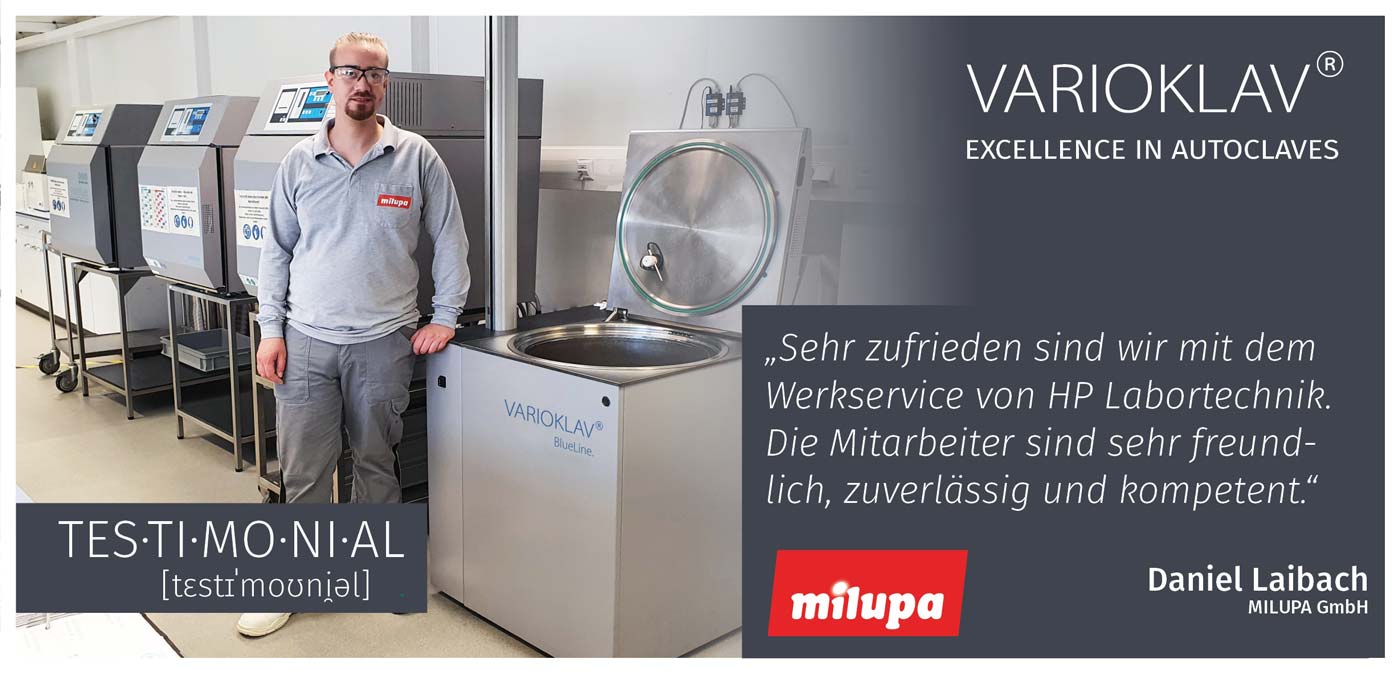
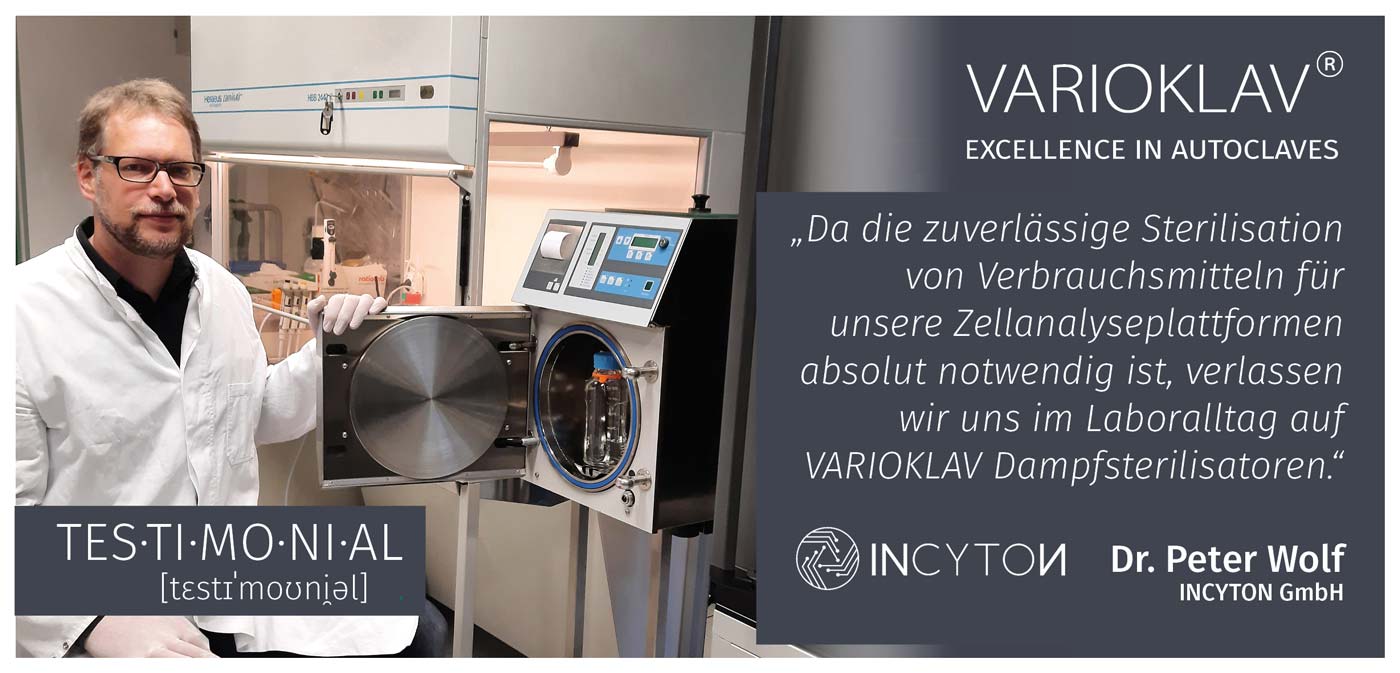
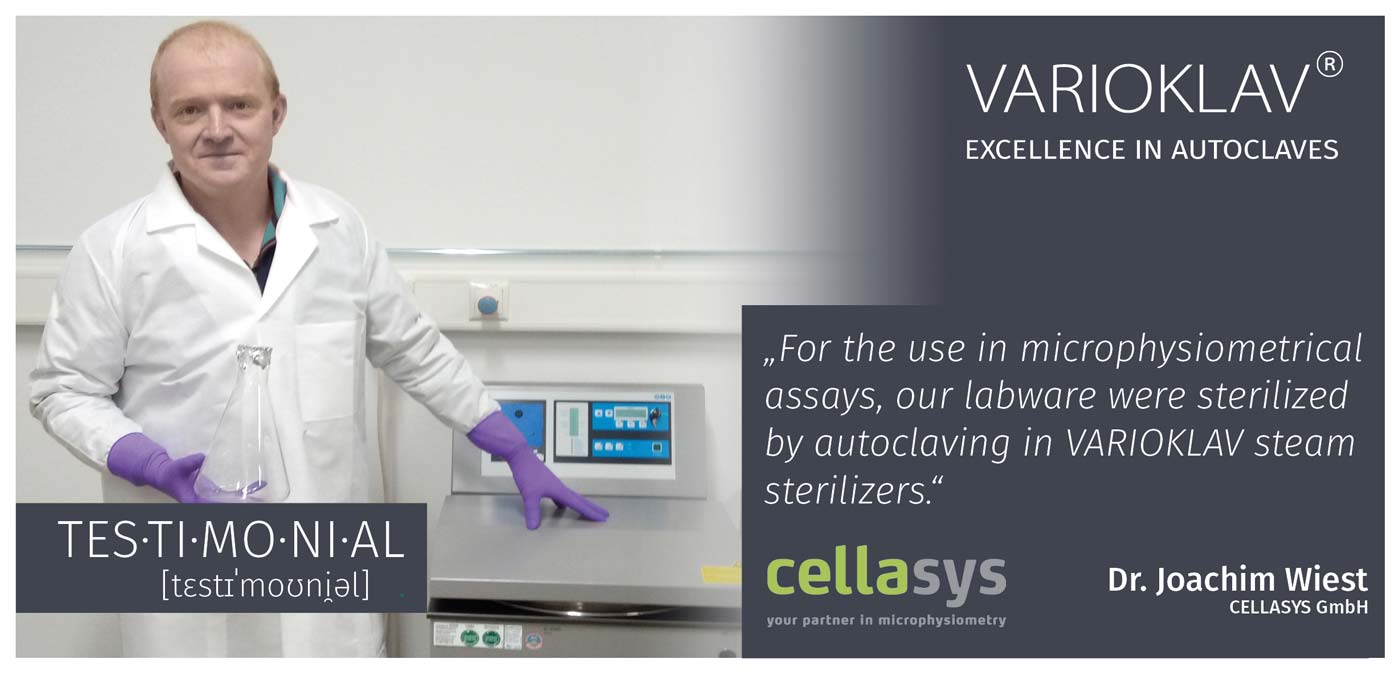
Varioklav Blueline equipment
Our VARIOKLAV® range includes floor-standing models with minimal footprint as well as compact benchtop autoclaves with capacities ranging from 25 to 195 litres.
Benchtop models
- Extremely handy depths of 810 or 890 mm, narrow design
- Multiple programme settings
- Flexibility and ease-of-use
- Automatic exhaust steam condenser
- Thermal lock meeting TRB 402 for liquids
- Programmable sterilisation cycles
- Shelves can be loaded into four height-adjustable positions
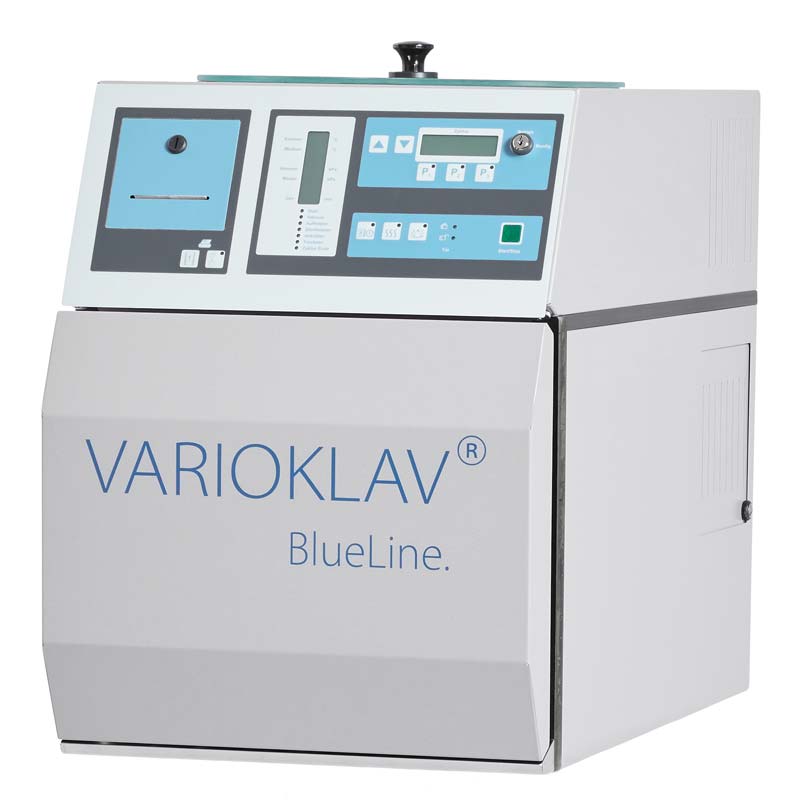
Floor-standing models
- Best possible usability comes from matching sterilisation basket and bottle sizes
- Capacity up to 175 litres
- Best possible steam generation with lift
- Advanced technical performance
- Sterilisation chamber free of heating elements and feed water.
- Thermal lock meeting TRB 402 for liquids
- Independent compressed air supply for seals control circuit, safety interlock and pneumatic control valves
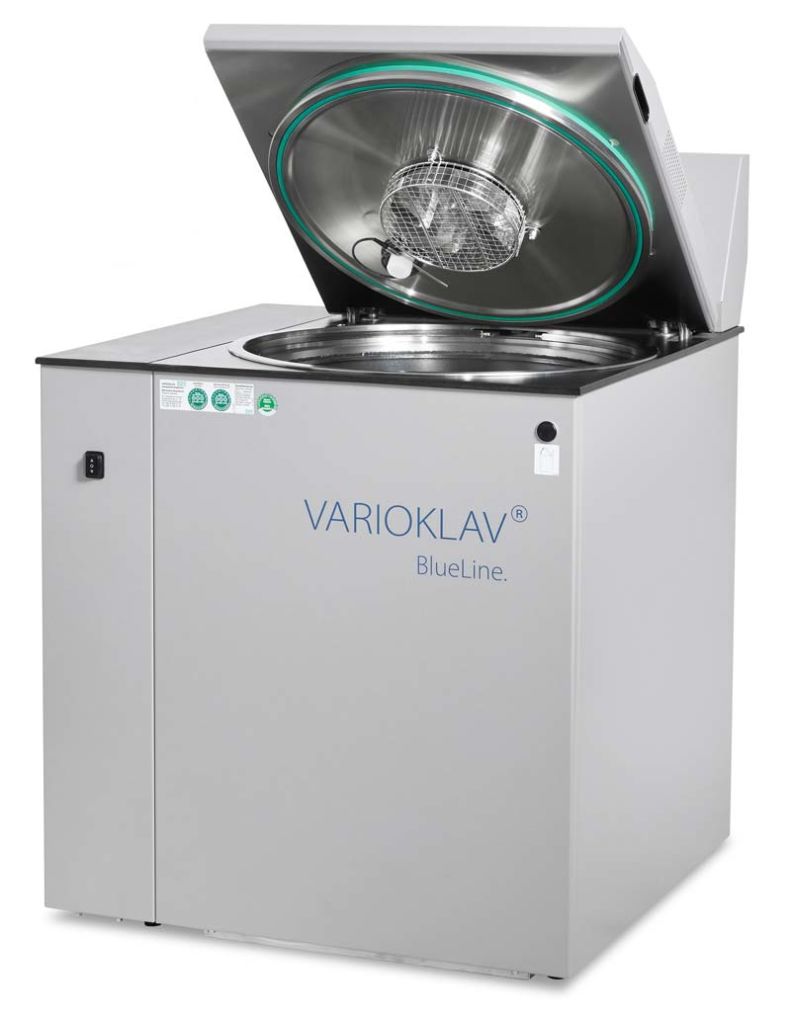
Frequently Asked Questions
Disinfection normally refers to the inactivation of pathogenic microorganisms and reduction in number of pathogens by at least five log levels. This means no more than 10 colony forming units (CFUs) out of 1,000,000 can survive the disinfection process.
By contrast, sterilisation is a process to remove all living microorganisms such as bacteria, fungi or viruses and their dormant phases from substances, objects and equipment. Accordingly, the goal of sterilisation is the complete removal of all pathogens including reproductive microorganisms from anything classed as sterile. Sterilisation is used for reprocessing medical apparatus, decontaminating infectious laboratory waste and for manufacturing sterile dosage forms and sterile disposable items for laboratory and clinical use.
In hospitals, medical centres, laboratories and manufacturing facilities in the food industry, it is important that certain areas and instruments are not only clean, but also absolutely sterile and therefore pathogen-free. Physical, physical-chemical and mechanical processes can be used to achieve this.
Steam sterilisers, dry heat sterilisers and radiation sterilisers are used in physical sterilisation processes. The material that needs to be sterilised is what determines the correct choice of sterilisation process: are the items that need to be sterilised thermostable or thermolabile? While anything in a dry heat steriliser has to withstand dry heat up to 200 Celsius, the steam steriliser works at up to just 130 Celsius using moist heat. Radiation sterilisers work using gamma, UV or X-rays and are therefore suitable for any substances which cannot be exposed to high temperatures.
Steam sterilisers use steam to kill pathogens. Steam sterilisers are therefore used in medicine and in biotechnology in particular, to sterilise or disinfect medical instruments, liquid nutrient media or glassware. Steam sterilisation is a reliable method for making heat-resistant plastic, rubber, metal, ceramics, glass or linen totally sterile within a relatively short period of time.
This works using saturated and superheated steam. This is done in steam sterilisation using a vacuum process (for example a Varioklav® GreenLine device or a Varioklav® BlueLine autoclave with vacuum module), to generate an initial vacuum, so that air present in the sterilisation chamber is totally evacuated. The water is then heated until the steam pressure in the autoclave reaches 2 bar at 121 degrees and saturated steam is produced.
Autoclaves are traditionally used in the fields of medicine, biotechnology and the manufacturing sector, for processing medical apparatus, such as in central sterile supply departments (CSSD) or medical apparatus processing departments, as well as in the production of medication or solutions in pharmacies.
The term autoclave can be used interchangeably with steam steriliser and generally refers to a gas-tight, sealable pressure vessel used for thermal treatment of substances under high pressure. When it comes to sterilisation in the medical technology, pharmaceutical and biotechnology sectors, a basic distinction is made between two sterilisation processes: the vacuum process and the flow or gravity process. In both cases, the total volume of the items or substances that need to be sterilised is specified in sterilisation units (StU), with one sterilisation unit corresponding to 54 litres. This unit is used to distinguish autoclaves as large steam sterilisers and small steam sterilisers:
Large steam sterilisers refers to all autoclaves with a capacity greater than or equal to one sterilisation unit as defined in DIN EN 285. Large autoclaves usually work using the vacuum process and are therefore suitable for the sterilisation and preparation of packed or unpacked, solid or porous medical apparatus with and without cavities. With large sterilisers, steam is usually generated by integrated electrical steam generators (internal steam source) or by an external wall steam system (external steam source).
As defined in DIN EN 13060, the definition of small steam sterilisers covers all autoclaves with a capacity below one sterilisation unit. Small steam sterilisers use one of three different types of sterilisation cycle:
Small steam sterilisers with class N sterilisation
Class N autoclaves work using the flow or gravity method. Air in the sterilisation chamber is displaced from the chamber by the steam flowing in. Due to the lack of vacuum, class N sterilisation cycles are only suitable for solid medical instruments out of their packaging, such as probes or forceps. Overall, class N sterilisers should only be used for non-critical medical apparatus where sterilisation is not a legal requirement. Following a class N sterilisation cycle, the sterile items are not suitable for transport or prolonged storage, but are only sterile for immediate use.
Small steam sterilisers with class S (specified) sterilisation
Class S autoclaves are suitable for reprocessing particular medical apparatus listed by the autoclave manufacturer in the cycle table. The properties of a class S steriliser must be tested by its manufacturer, and defined, validated and approved for each relevant application. Type S autoclaves can also be used to sterilise solid intruments out of their packaging which are not used for surgical procedures.
Small steam sterilisers with class B (big) sterilisation
The class B sterilisation cycle is generally considered to be the safest method of sterilisation and ensures that the widest variety of sterile items are sterilised and reprocessed as appropriate for clinical applications. With regard to cycle selection, class B sterilisers – unlike classes N and S – do not require any separate staff training.